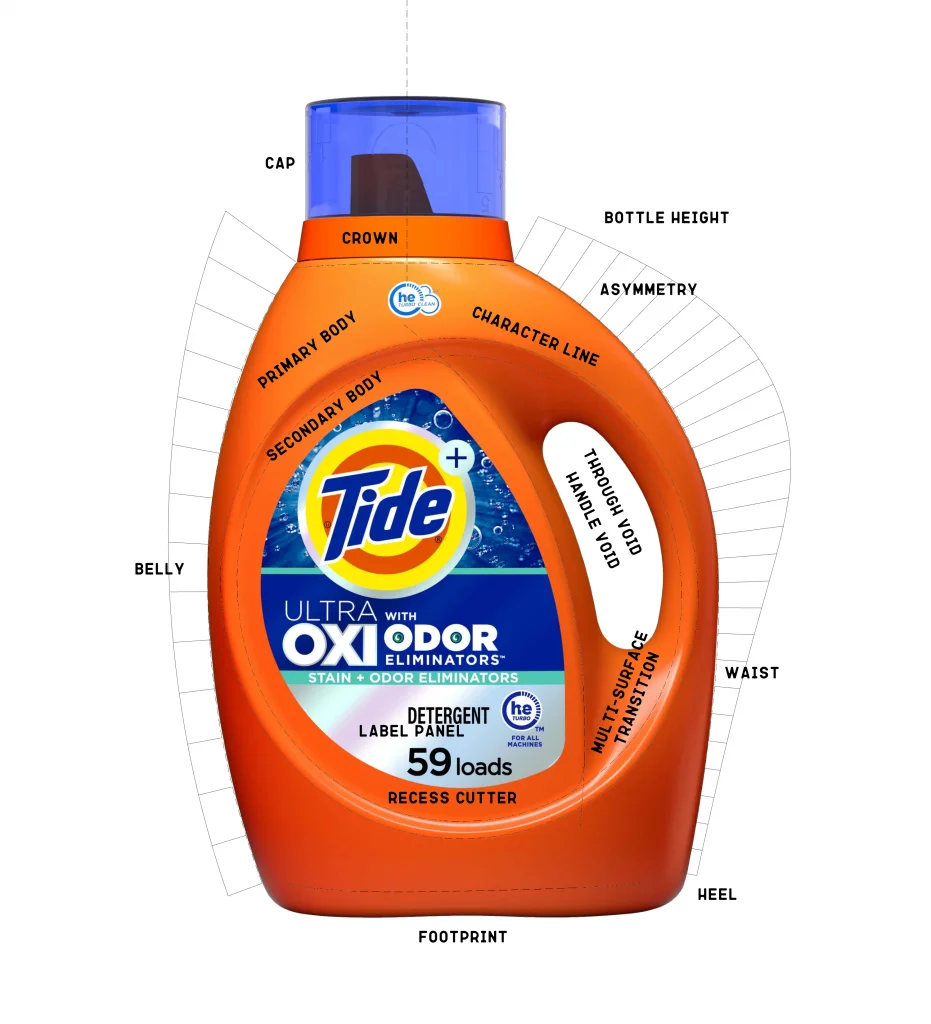
The Deceptive Simplicity of Designing: A Detergent Bottle, Lesson in Surface Modeling and Human Perception of Complexity
When I first approached the task of designing a 3D model of a detergent bottle as a skill challenge, I anticipated a straightforward exercise in surface modeling. The form appeared simple enough: a primary volume, a handle, and a few surface details. With the 2D brief in hand, I created a reasonable facsimile of the bottle’s shape within an hour. It looked acceptable—even accurate—at first glance, and I felt confident in my progress.
However, as I began to consider the topology and how to describe it, I realized my initial understanding of the form was, well, incomplete. What I had dismissed as a simple object revealed layers of complexity I hadn’t anticipated—subtle curves, ergonomic considerations, and design nuances that my first attempt had glossed over. It was a humbling reminder that even the most mundane objects can defy our assumptions and reveal hidden depths. To someone more experienced in the field, my early confidence might have come across as the enthusiasm of a dilettante—someone skimming the surface without fully grasping the intricacies beneath. What began as a technical challenge evolved into a lesson in the complexities of design and the importance of looking beyond first impressions.
Soap Bottle, Fast Manual Build from AI Gen by Stratospheric on Sketchfab
The Illusion of Simplicity
Surface modeling, at its core, requires an understanding of mathematical forms and the ability to achieve seamless surface continuity—how surfaces flow into one another. How a CAD program is directed to build these surfaces and arrive at these complex geometric relationships is a learned and practiced skill. These technical necessities for manufacturing a product for industry define its value, functionality, and aesthetic appeal. At first glance, a detergent bottle seems to be an exercise in basic positive and negative volumes: a main body, a handle, and perhaps a few surface details. For an experienced surface modeler, this should be a manageable task.
My initial approach followed this logic. I broke down the form into primary volumes defined by minimal surfaces, governed by the geometric constraints of the silhouette. The first model I created matched the 2D brief reasonably well. I uploaded it to Sketchfab as a high-resolution mesh in a reflective material. Skill exercise mission accomplished! But as I began to reflect on the surface framework and develop a mental parametric model, I realized a surprising depth of complexity. What I had assumed to be a simple form revealed itself as a sophisticated interplay of geometry, functionality, and brand identity.
The Hidden Language of Design
As I systematically deconstructed the bottle’s form, I realized that professional bottle design is a domain with its own specialized vocabulary. While the deeper vocabulary of any design is invisible to the user, every aspect of the form—body proportions, handle integration, neck architecture, base geometry, and even surface character lines—can have specific terminology for experts or specialists in the field. These terms have likely evolved over decades of manufacturing and design practice, encapsulating not just geometric definitions but also functional requirements, design intent, and brand identity.
My initial model, while technically accurate, captured only a visible form. It failed to account for the deeper layers of meaning embedded in each design decision. For example, the handle’s void isn’t just a negative space; it’s a carefully calculated feature that balances ergonomics, visual appeal, and manufacturing feasibility. Similarly, surface details aren’t merely decorative; they reflect light in specific ways, guide the user’s hand, and reinforce brand recognition. The body is not simply a volume; it is an interplay of positive and negative volumes and transitions that add character.
A Masterclass in Surface Intelligence: The Tide Bottle
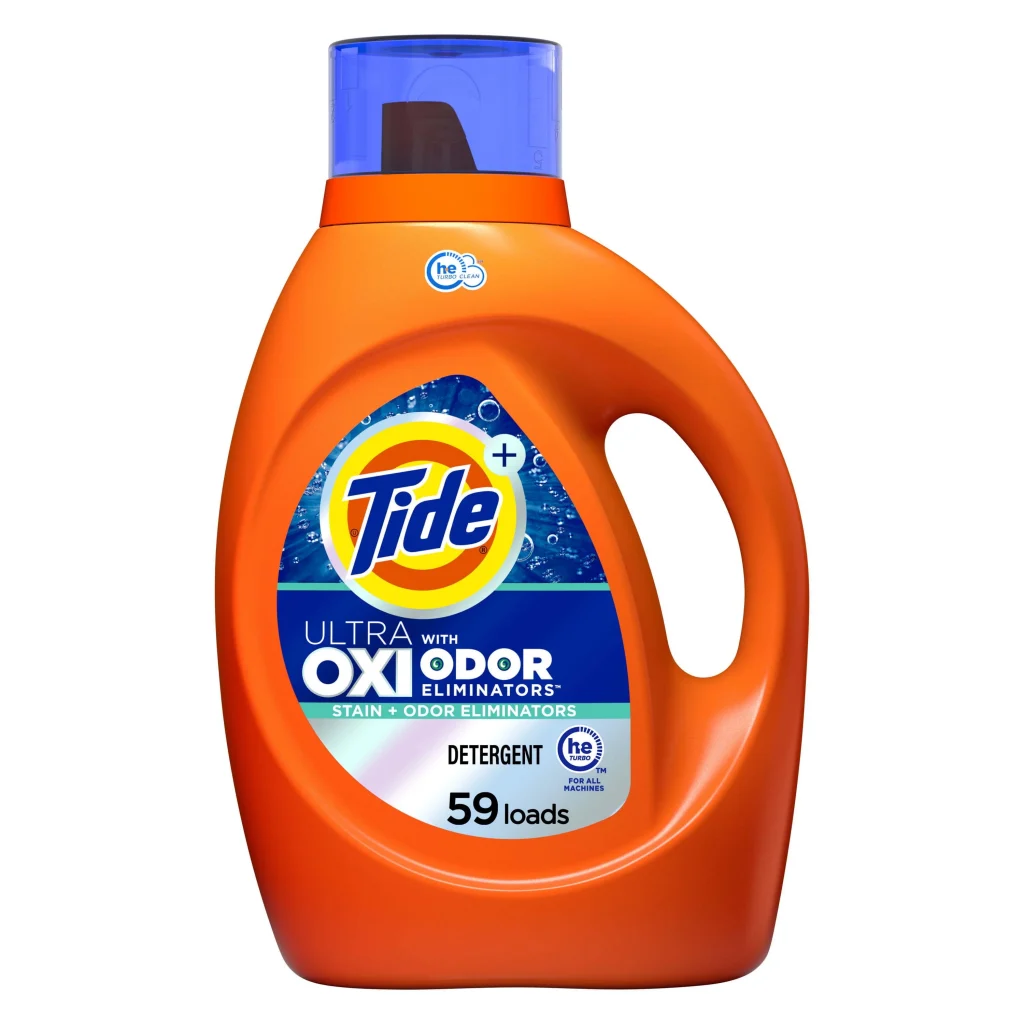
The Tide detergent bottle is a perfect example of this multilayered complexity. Its main body employs revealed sub-surfaces that maintain industry-standard continuity while creating distinct character lines. These lines aren’t just aesthetic; they serve functional purposes, such as reflecting light in calculated ways, framing printed labels, and guiding the user’s grip. The front face’s circular geometry character is particularly ingenious—it echoes both the brand’s logo and the form of a front-loading washing machine door, creating a subtle visual dialogue between the product and its purpose.
The handle, too, is a marvel of design. Its void penetrates the main mass with precision, its boundaries defined by ergonomic requirements and visual balance. Every curve, every surface, and every detail is the result of a deliberate decision-making process that considers manufacturing constraints, user experience, and brand identity.
Implications for AI and the Future of Design
This realization has enlightening implications, especially in the context of current advancements in artificial intelligence. There’s a growing ambition to generate 3D geometry from natural language descriptions, assuming that form can be fully captured through text. However, the example of bottle design reveals a significant gap between geometric description and the specialized vocabulary needed to convey design intent. The commonality of form language is not a given—what one designer calls a “flare,” another might call a “taper.” Similarly, terms like “undercut,” “fillet,” or “chamfer” can carry different nuances depending on the context or industry. Among expert designers, there exist lexicons and glossaries that vary from company to company. The critical aspect is that many surface decisions may go without every being explicitly named. They are executed in other modes of brainpower than language.
Each term in the professional design lexicon carries multiple layers of meaning: geometric constraints, surface character, tactile qualities, and market-appropriate complexity. Surface intelligence, in this context, requires a delicate balance—surfaces must project sophistication without appearing overwrought, and value without suggesting cheapness through oversimplification. This level of nuance is difficult to articulate in natural language, let alone translate into a 3D model. Modeled 3D surfaces are evaluated by the simulated movement of light and reflection on a screen, followed by a combination of light observations and the feel of surfaces under the hand in fabricated prototypes.
Conclusion: The Complexity Beneath the Surface
What began as a simple modeling exercise became a humbling reminder of the depth and complexity inherent in even the most ordinary objects. Designing a detergent bottle is not just about creating a shape; it’s about understanding the intricate interplay of form, function, and brand identity. It’s about recognizing that every curve, every line, and every surface carries meaning—a meaning that is often invisible to the untrained eye. This realization raises the bar for expectations that LLMs can account for the complexities of physical objects, as well as the effort required by a system prompter to articulate what is desired.
This experience has taught me to approach new design challenges with renewed humility and a systematic curiosity for surfaces. It has also made me skeptical of the assumption that natural language can fully capture the richness of design intent—especially as the degree of difficulty in description rises exponentially with the interactions of shapes. Yet, as we continue to explore the possibilities of AI in design, we must remember that true innovation lies not in simplifying complexity but in embracing it. In this case, AI proves to be a valuable complement, workshopping descriptions and terms to better define shapes and their interactions.
This leads into two different paths of exploration to be pursued in future posts.
A universal shape descriptor language. Does it exist in sections in different industries, where are some subsets?
Working shape glossary for a detergent bottle shape in conjunction with various LLMs:
FORM FUNDAMENTALS
- Parting Line: The seam where mold halves meet in manufacturing
- Draft Angle: Wall slope required for mold release
- Bosses: Reinforced areas supporting structural integrity
- Undercut: Area where form geometry prevents straight mold pull
- Through-Handle: Handle design that fully penetrates main body
- Void: Negative space created by handle penetration
- Mass: Primary volume of container
- Footprint: Base contact surface area
- Topology: Study of geometric form properties
- Profile: Side view silhouette
SURFACE ANATOMY
- Character Line: Distinct form line defining surface transition
- Crown: Top section of bottle including closure
- Shoulder: Transitional area between body and neck
- Waist: Narrowest circumference of body
- Heel: Transition from body to base
- Belly: Widest circumference of body
- Label Panel: Recessed area for label placement
- Relief: Depth of surface feature from reference plane
- Recess: Intentional depression in surface
- Chamfer: Angled corner transition
- Fillet: Rounded corner transition
- Blend: Smooth transition between surfaces
- Highlight Line: Surface feature that catches light
- Witness Line: Visible trace of manufacturing process
GEOMETRIC ELEMENTS
- Compound Curve: Surface with multiple radius changes
- Radius: Measure of curve arc
- Tangent: Point where curve meets straight line
- Inflection Point: Location where curve direction changes
- Centerline: Primary axis of symmetry
- Reference Plane: Base geometric surface
- Cross-section: Cut view showing internal profile
- Elevation: Straight-on view of any side
- Datum: Reference point for measurement
- Concave: Inward-curving surface
- Convex: Outward-curving surface
- Profile Radius: Edge curvature in silhouette
- Sweep: Continuous surface following a path
- Loft: Surface transitioning between profiles
STRUCTURAL FEATURES
- Gusset: Reinforcing structure
- Rib: Structural reinforcement feature
- Wall Section: Material thickness
- Node: Junction point of multiple features
- Load Path: Force distribution route
- Stress Concentration: Area of focused force
- Moment: Rotational force consideration
- Compression Zone: Area handling stacking load
- Transfer Ring: Neck reinforcement feature
- Support Structure: Internal strengthening geometry
FUNCTIONAL ELEMENTS
- Pour Angle: Optimal tilt for dispensing
- Grip Ergonomics: Handle interaction design
- Anti-rock Feature: Base stability design
- Stack Height: Vertical storage efficiency
- Neck Finish: Closure attachment detail
- Thread Form: Closure engagement design
- Vent: Air replacement feature
- Drain Back: Product recovery feature
- Dosing Feature: Measurement provision
- Label Panel: Information display area